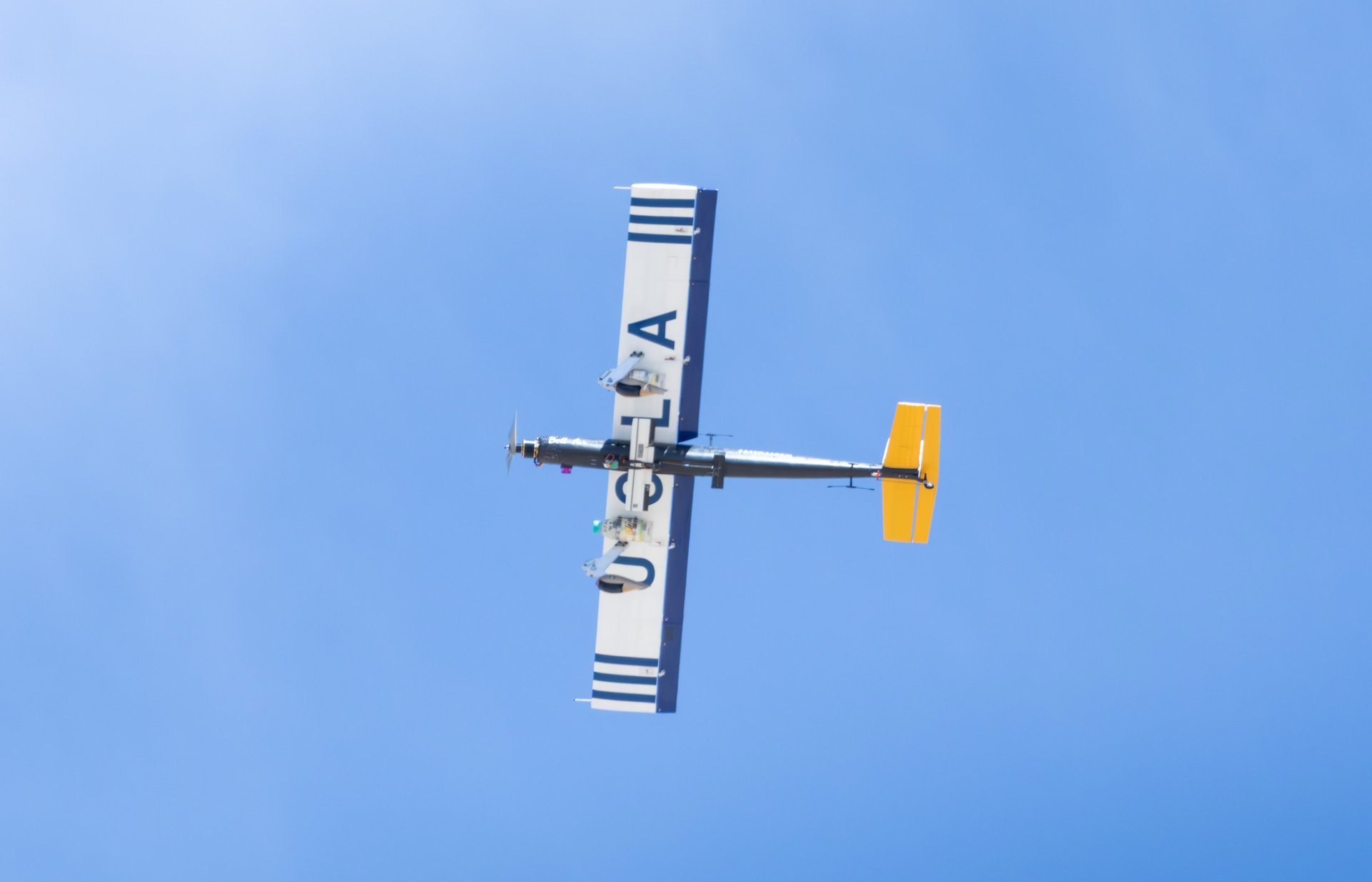
Subteams
Click to learn more about each of our six technical subteams.
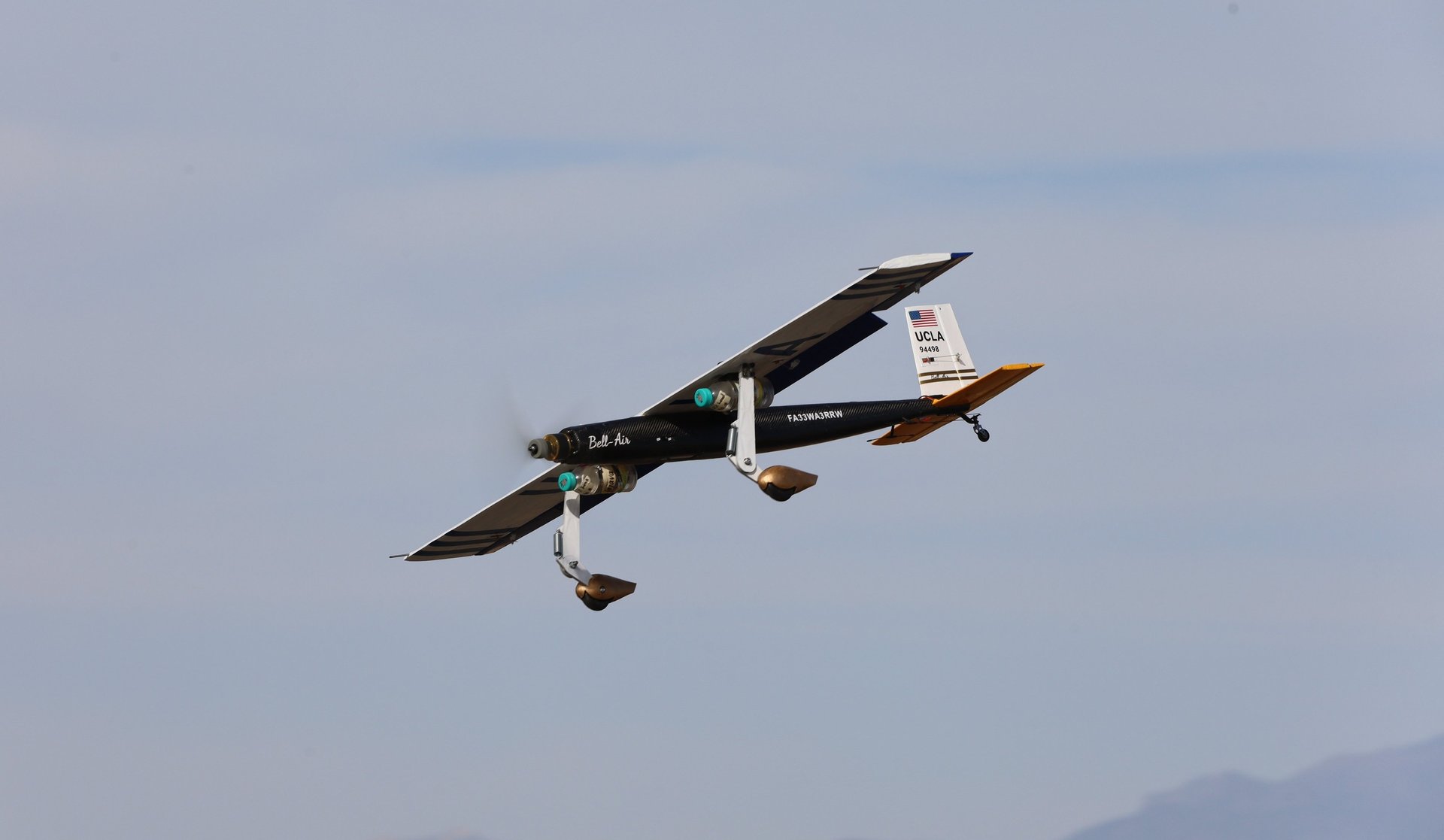
Aerodynamics
The Aerodynamics subteam is responsible for determining the configuration and dimensions of the aircraft required to best perform the competition missions and to maintain controlled flight. This includes a scoring analysis of the competition rules, sizing and stability calculations, airfoil selection, computational fluid dynamics (CFD) simulations, and wind tunnel tests.
If you are interested in understanding the forces behind flight as well as the specific designs that are most efficient when optimizing for certain features, aerodynamics is for you! If you like to code, run performance analysis tests, and make fancy plots, then you should join Aerodynamics.
Scoring Analysis
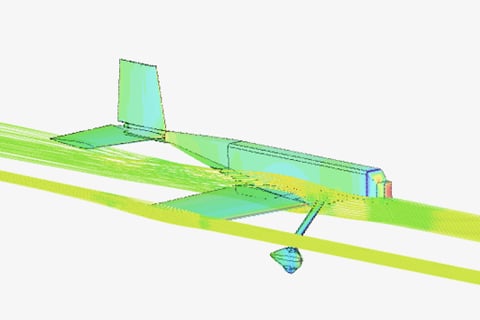
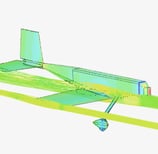
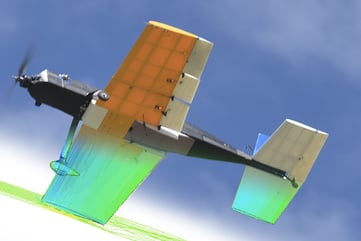
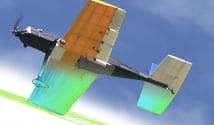
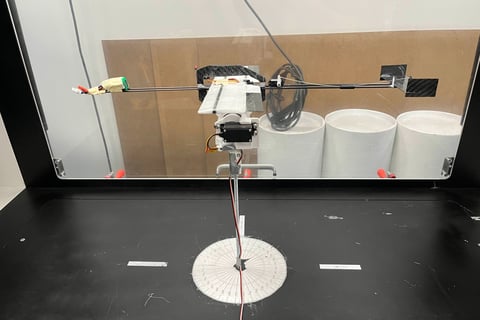
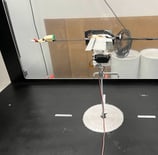
Sizing and Stability Calculations
Subteam members determine the configuration and dimensions of the aircraft to ensure that the plane will be capable of flight, easy to control, and able to accomplish all of the required missions. This is done using hand calculations to promote a thorough understanding of the process, as well as with MATLAB code to easily optimize the design.
A MATLAB code is used to analyze the scoring of each mission, as laid out in the competition rules, in order to determine which missions are the most critical and which aspects of the design should be focused on to maximize the overall competition score.
Airfoil Selection
The Aerodynamics subteam selects the cross-sectional profiles of the wing and other aerodynamic elements, using data and plots to determine which shape will be the most effective. This is done both manually to promote understanding, and using a Python script for optimization.
CFD and Wind Tunnel
CFD software is used to model how the aircraft will behave in flight, how much force is generated by each surface, and how efficiently the plane flies. The results of these simulations are used to improve the design and to provide data to other subteams. The CFD simulations are also validated using data collected by testing components in the UCLA wind tunnel, which gives us better insight into how our designs will behave in the real world.
Half-Plane CFD Showing Streamlines Over the Wing
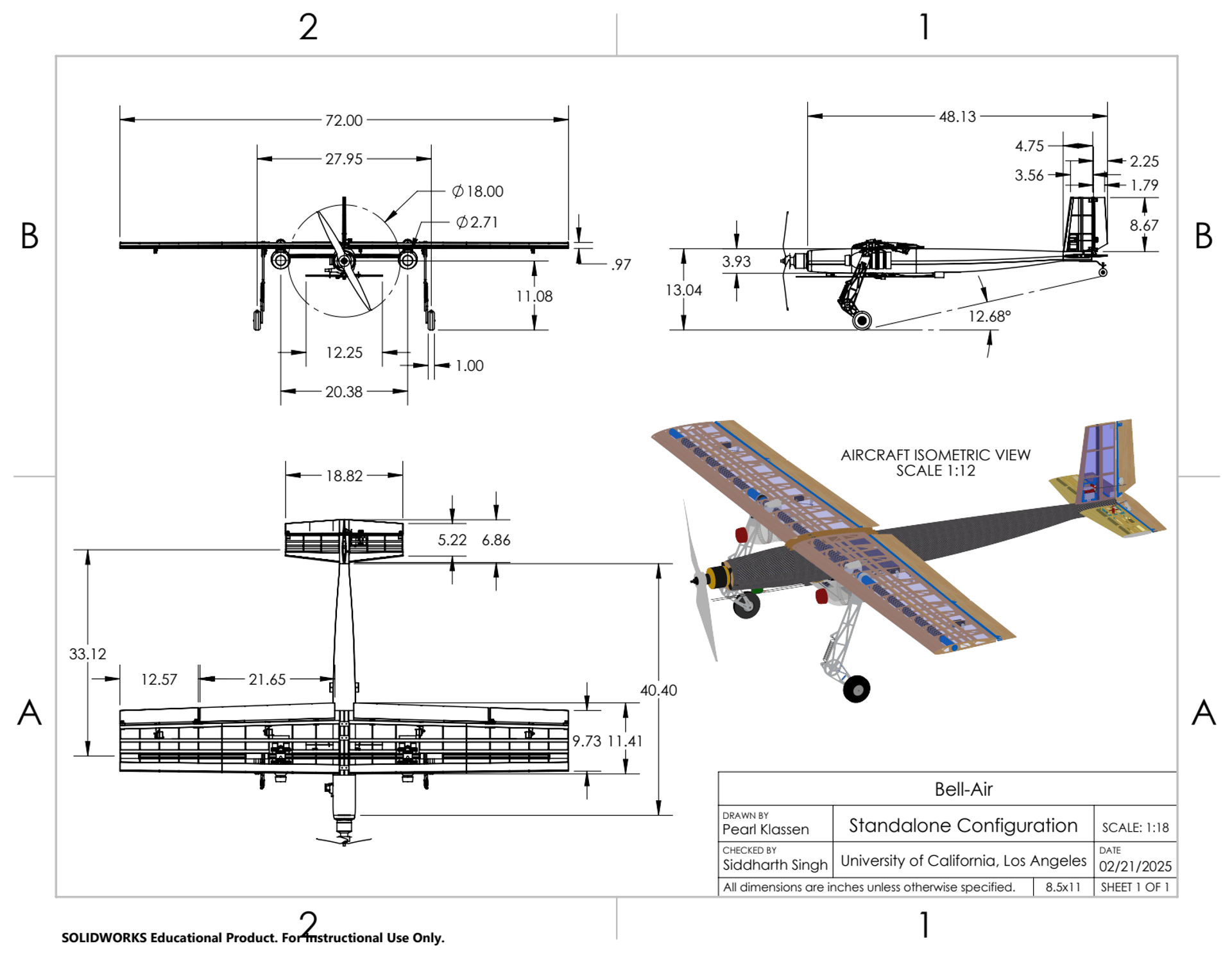
CAD
The CAD subteam builds a 3D model for the plane based off of the sizing from the aerodynamics subteam using Solidworks, which is then referenced during manufacturing. Additionally, CAD is responsible for designing and constructing new, unique parts on a case-by-case basis for manufacturing. This is an exciting way to see your work on display on the final competition plane!
If you love to work independently, thinking of new and innovative solutions to never-before encountered problems, then the CAD subteam is perfect for you! You will be able to contribute directly to the creation of the competition plane and aid Manufacturing in quickly producing new mechanisms.
Plane Development
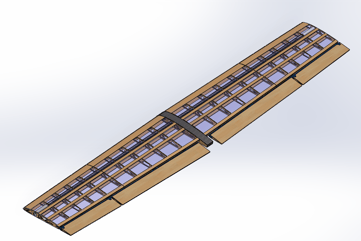
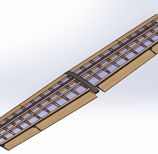
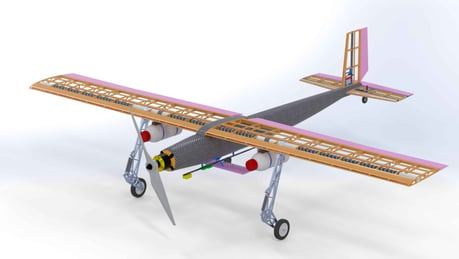
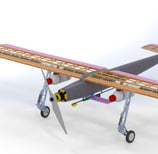
The CAD design provides a preview of the plane before it is built. The team transforms conceptual designs into detailed plans, utilizing both technical knowledge and innovative thinking. The design is used to create jigs and molds for the creation of parts, as well as for some parts to be 3D-printed from the design directly.
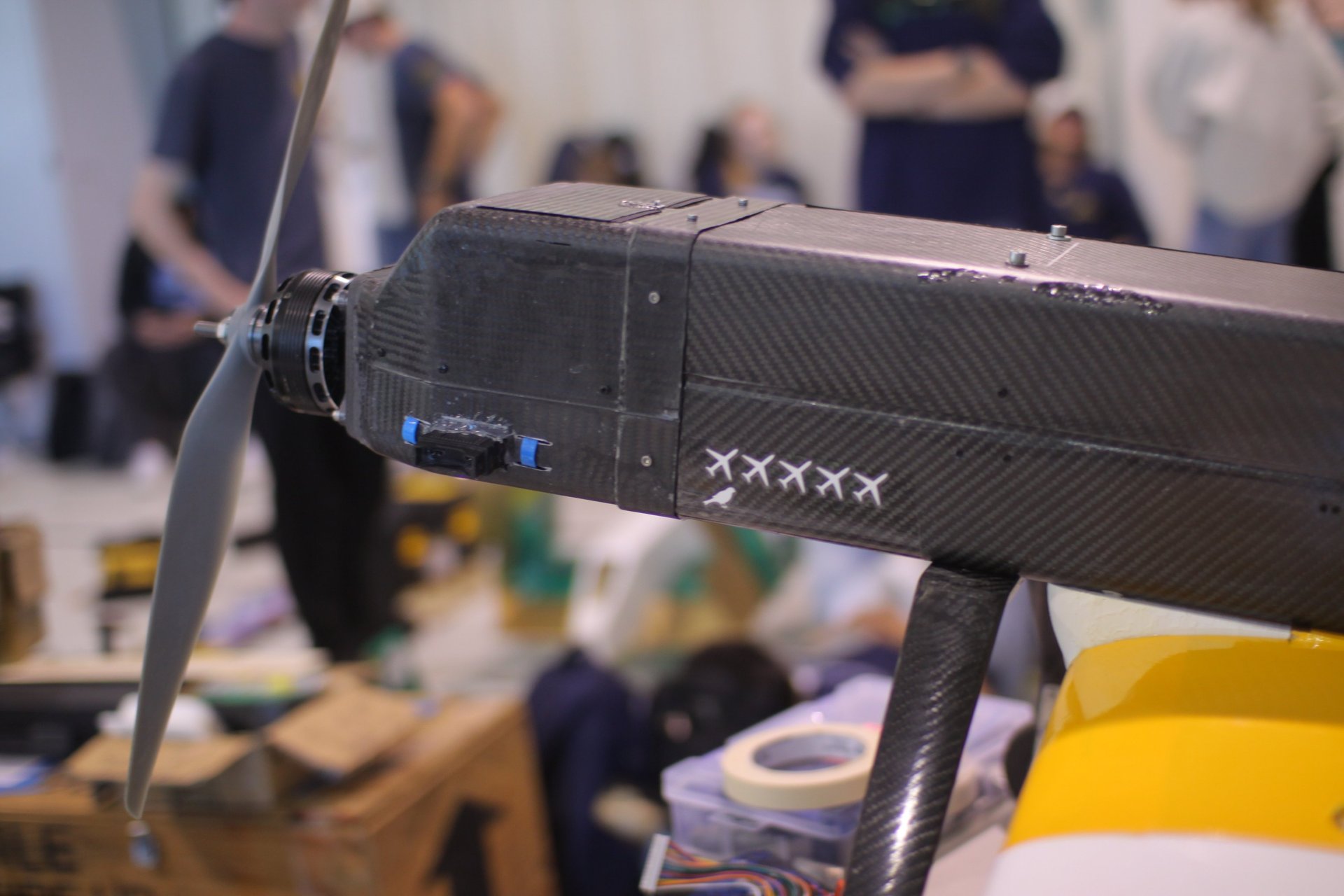
Manufacturing
The Manufacturing team is responsible for constructing the plane. This includes wet carbon fiber layups, 3D printed frameworks, laser-cut balsa, and innovative designs that are catered specifically to our plane.
Manufacturing involves hands-on work, thinking outside the box, and (sometimes) last minute fixes and repairs. If you're interested by the idea of physically constructing our competition plane, then this subteam is definitely for you!
Fly Day Responsibilities
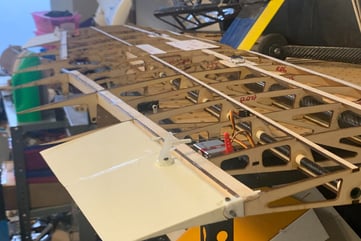
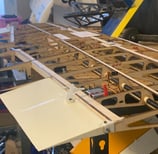
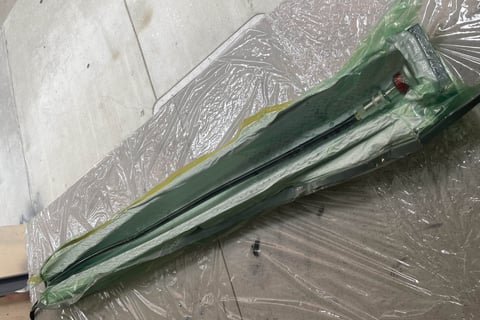
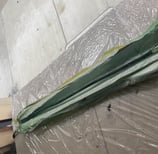
On Fly Days, it is essential that the manufacturing subteam ensures that the plane is ready to fly; some responsibilities include assembling the modular components, connecting wiring, and covering all hatches securely. Packing lists also need to be written and followed so that we have all necessary tools and equipment to repair the plane at the airfield if necessary.
The Manufacturing team is responsible for constructing the plane. This includes wet carbon fiber layups, 3D printed frameworks, laser-cut balsa, and innovative designs that are catered specifically to our plane.
Manufacturing involves hands-on work, thinking outside the box, and (sometimes) last minute fixes and repairs. If you're interested by the idea of physically constructing our competition plane, then this subteam is definitely for you!
Manufacturing
Fly Day Responsibilities
On Fly Days, it is essential that the manufacturing subteam ensures that the plane is ready to fly; some responsibilities include assembling the modular components, connecting wiring, and covering all hatches securely. Packing lists also need to be written and followed so that we have all necessary tools and equipment to repair the plane at the airfield if necessary.
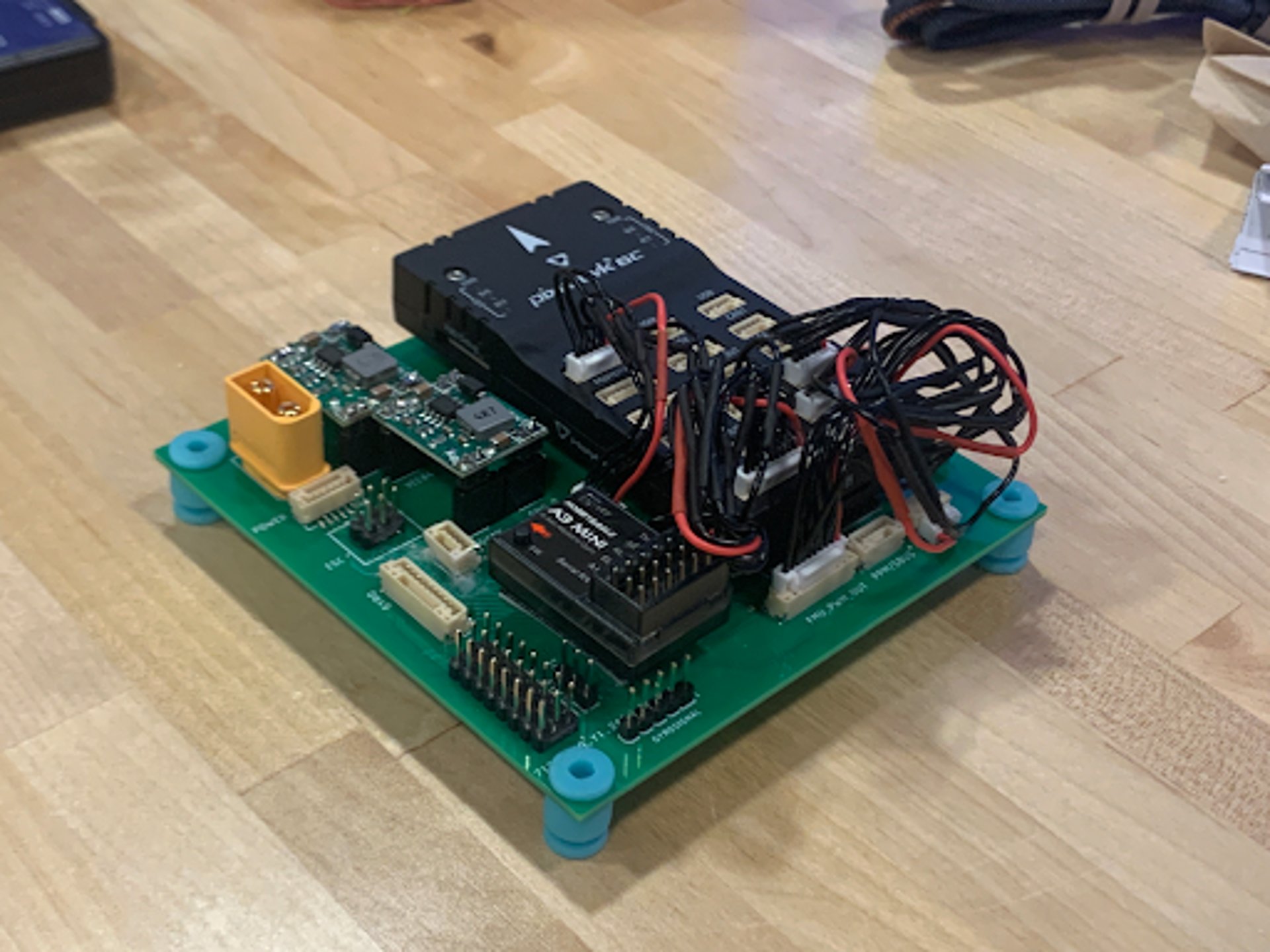
Propulsion & Electronics
The Propulsion & Electronics team is responsible for selecting and testing the electric propulsion system components for the aircraft. We also set up any other electronics for the aircraft, such as servo actuators and the receiver/transmitter.
The Propulsions subteam is the reason the plane flies! Isn't that fun? Jokes aside, choosing the correct propeller is vital to having a good flight. If electronics interest you, then this subteam is definitely the right one.
Fly Day Responsibilities
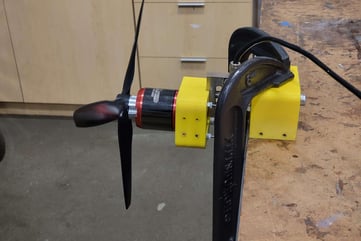
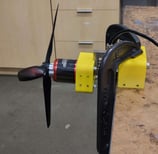
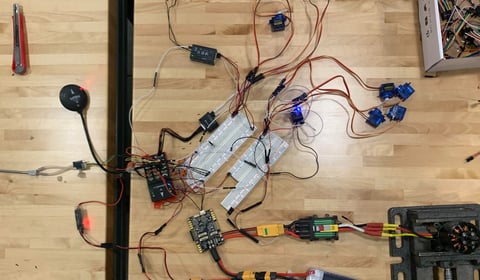
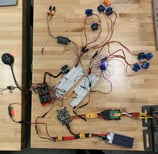
Before flight, the propulsions and electronics team selects the appropriate propeller and tests the response of the servos that power the control surfaces (flaps, ailerons, elevator and rudder) and other mechanisms, such as our banner deployment mechanism last year.
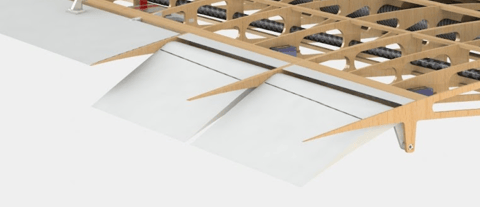
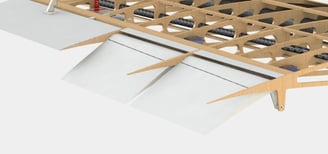
Testing Methods
We rely on a mixture of theoretical and practical methods to test the propulsion systems, including static thrust testing in the lab. The propulsion and electronics subteam relies on software such as MATLAB and eCalc to aid with the design and implementation of the propulsion and electronics systems.
Propulsion & Electronics
The Propulsion & Electronics team is responsible for selecting and testing the electric propulsion system components for the aircraft. We also set up any other electronics for the aircraft, such as servo actuators and the receiver/transmitter.
The Propulsions subteam is the reason the plane flies! Isn't that fun? Jokes aside, choosing the correct propeller is vital to having a good flight. If electronics interest you, then this subteam is definitely the right one.
Fly Day Responsibilities
Before flight, the propulsions and electronics team selects the appropriate propeller and tests the response of the servos that power the control surfaces (flaps, ailerons, elevator and rudder) and other mechanisms, such as our banner deployment mechanism last year.
Testing Methods
We rely on a mixture of theoretical and practical methods to test the propulsion systems, including static thrust testing in the lab. The propulsion and electronics subteam relies on software such as MATLAB and eCalc to aid with the design and implementation of the propulsion and electronics systems.
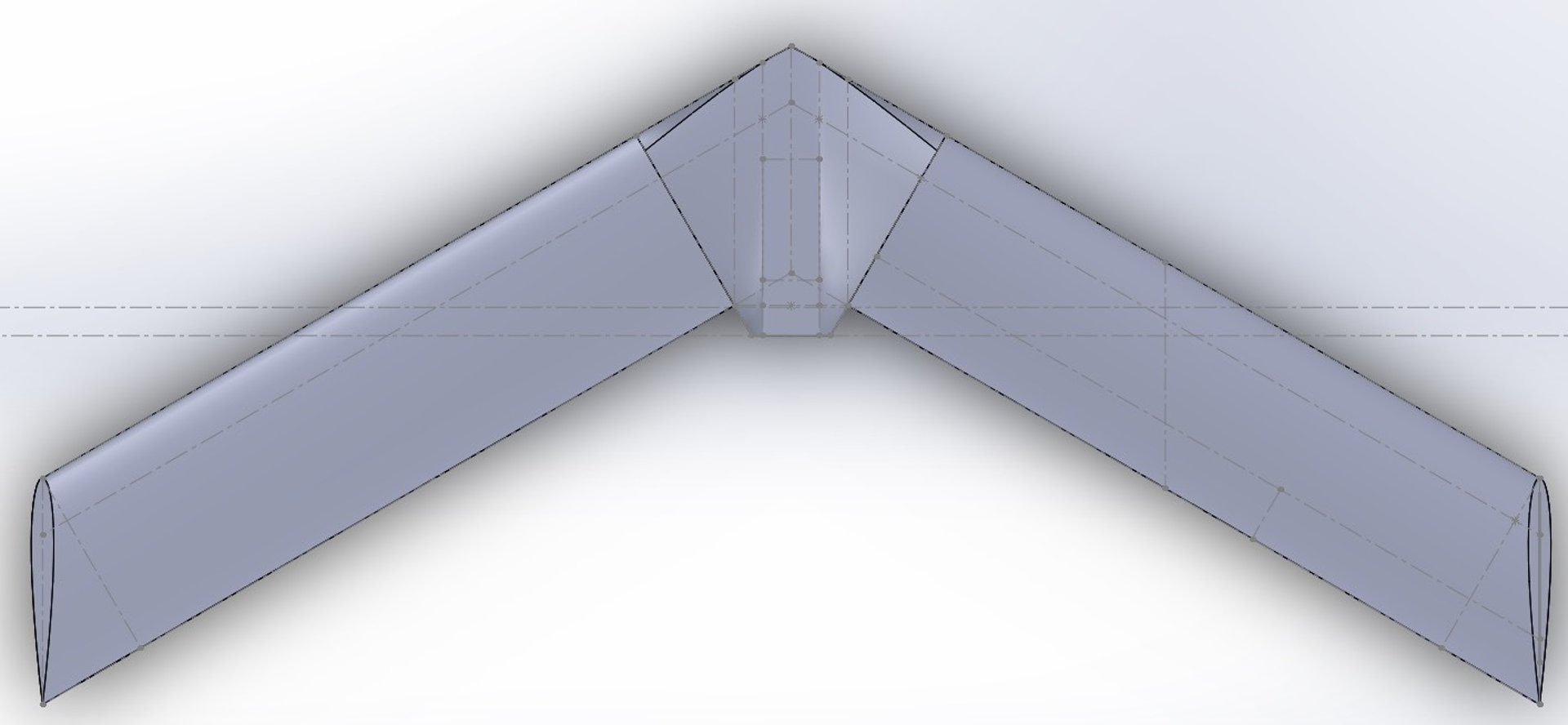
Research & Development
The R&D team works to expand our base of knowledge, looking into new plane designs, analysis methods, and materials and manufacturing processes to support current and future projects. This way, our team continuously improves and achieves the best possible design based on the yearly competition.
If you enjoy researching and pushing the limits of what is possible, then you definitely belong on R&D! You will be funded and lead a group in researching your innovative idea, and you will have a great time contributing to DBF!
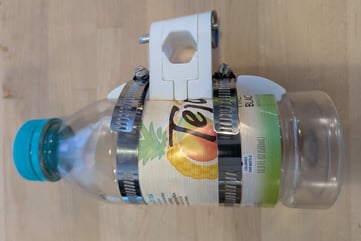
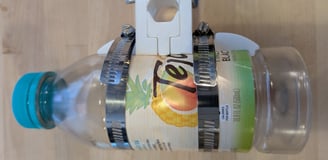
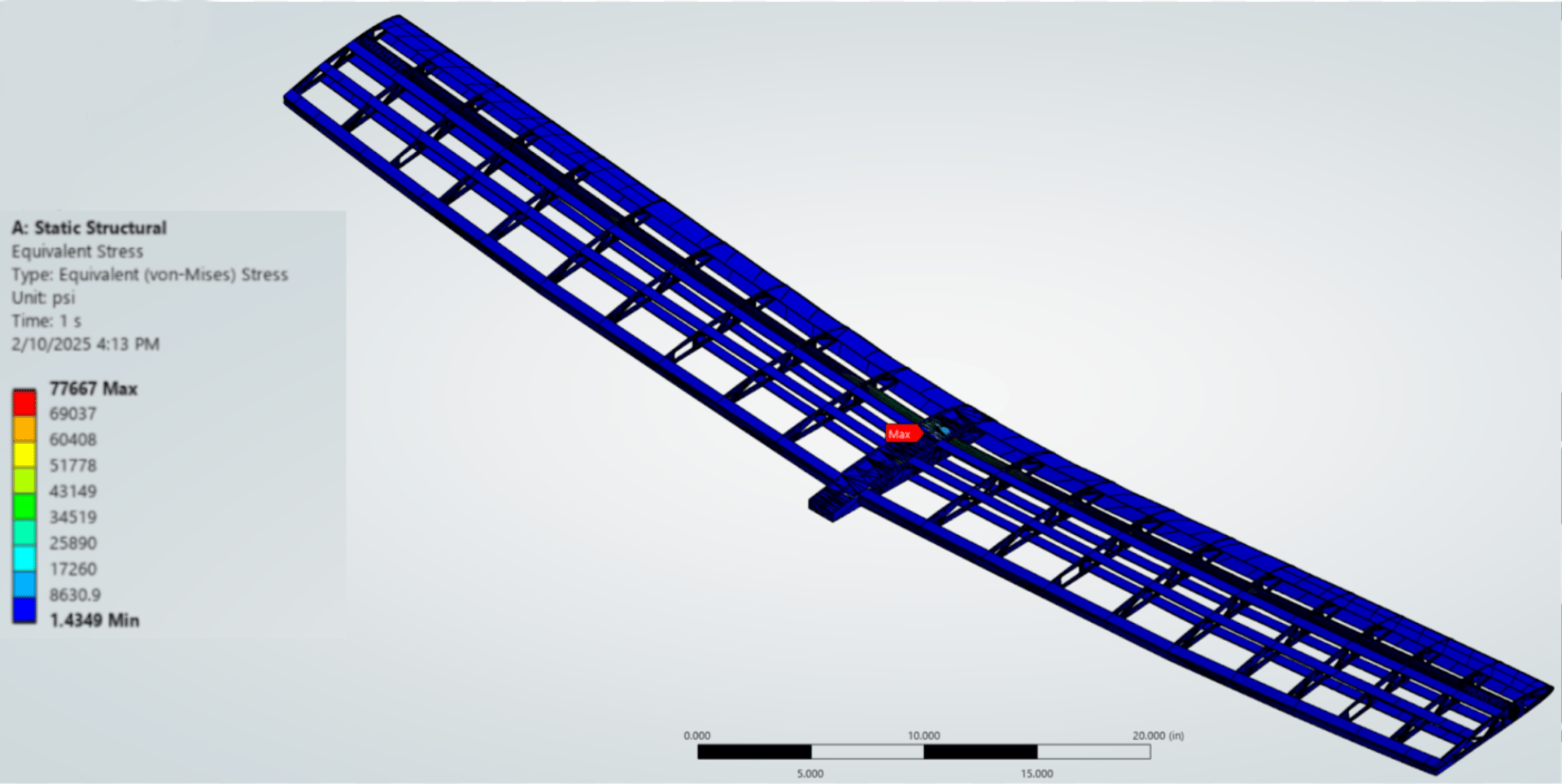
Structures
The Structures subteam is responsible for analyzing the plane structures to ensure that they can support the required loads. Areas of focus include spar sizing, lightening hole placement, generative design, and material selection.
This year, the Ground Mission involves balancing the plane by the wingtips and placing weight on the fuselage. If you want to see our plane hold strong against these loads and you are interested in designing an intricately light plane, then this subteam is for you!
Key Tools
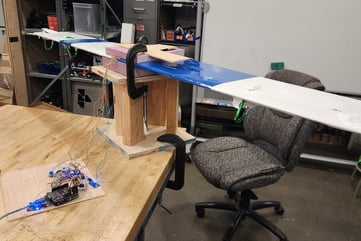
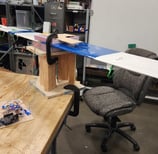
The team works with Finite Element Analysis (FEA) tools in Ansys to ensure that expected loads will not cause excessive deformation or stresses. Generative design will also be utilized this year to optimize a lighter plane and remove weight wherever it is not necessary for structure.
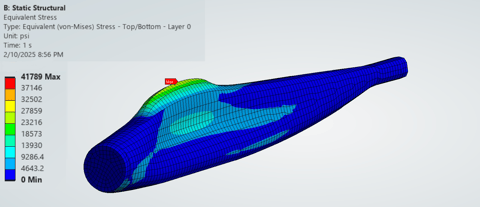
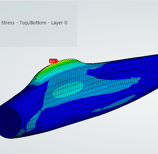
Structures
The Structures subteam is responsible for analyzing the plane structures to ensure that they can support the required loads. Areas of focus include spar sizing, lightening hole placement, generative design, and material selection.
This year, the Ground Mission involves balancing the plane by the wingtips and placing weight on the fuselage. If you want to see our plane hold strong against these loads and you are interested in designing an intricately light plane, then this subteam is for you!
Key Tools
The team works with Finite Element Analysis (FEA) tools in Ansys to ensure that expected loads will not cause excessive deformation or stresses. Generative design will also be utilized this year to optimize a lighter plane and remove weight wherever it is not necessary for structure.